Истиратели дисковые
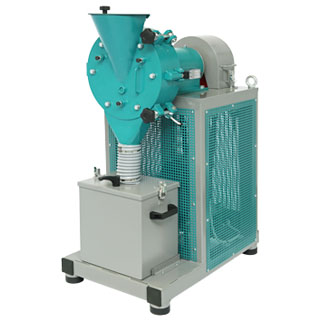
Назначение
Истиратели дисковые предназначены для измельчения проб сыпучих материалов до тонкодисперсного состояния. В истирателях дисковых измельчение происходит за счет истирания – одновременной деформации сжатия и сдвига частиц материала между неподвижным и подвижным дисками. Крупность измельченного продукта регулируется величиной зазора между дисками (щели) и физическими свойствами материала.
Истиратели дисковые, Истиратель дисковый ИД 65, Истиратель дисковый ИД 175М, Истиратель дисковый ИД 175, Истиратель дисковый ИД 200, Истиратель дисковый ИД 250
Истиратель дисковый ИД 65. Руководство по эксплуатации.
Истиратель дисковый ИД 175. Руководство по эксплуатации.
Истиратель дисковый ИД 175М. Руководство по эксплуатации.
Истиратель дисковый ИД 200. Руководство по эксплуатации.
Истиратель дисковый ИД 250. Руководство по эксплуатации.
Истиратели дисковые: Истиратель дисковый ИД 65, Истиратель дисковый ИД 175М, Истиратель дисковый ИД 175, Истиратель дисковый ИД 200, Истиратель дисковый ИД 250
Характеристики | ИД 65 | ИД 175М | ИД 175 | ИД 200 | ИД 250 |
---|---|---|---|---|---|
Размеры загрузочного окна, мм | Ø 50 | 80х165 | 95х185 | 95х185 | 95х185 |
Размер загрузочного окна, мм | Ø 11 | 11х57 | 11х71 | 11х71 | 18х75 |
Крупность исходного материала, мм, не более* | 3 | 4 | 4 | 4 | 4 |
Твердость измельчаемого материала, не более | 8 ед. по Моосу | 8 ед. по Моосу** | 8 ед. по Моосу** | 8 ед. по Моосу** | 7 ед. по Моосу |
Диапазон регулировки разгрузочной щели, мм | 0,05 - 2 | 0,07 - 5 | 0,1 - 5 | 0,1 - 5 | 0,1 - 5 |
Размер частиц продукта измельчения при минимальной щели, мм | 90%<0,05 | 90%<0,071 | 90%<0,1 | 90%<0,1 | 90%<0,1 |
Производительность, кг/ч, не более* | 5 | 50 | 100 | 150 | 300 |
Мощность электродвигателя, кВт | 0,37 | 2,2 | 2,2 | 2,2 | 4 |
Напряжение питания, 50 Гц, В | 220 | 380 | 380 | 380 | 380 |
Полный / полезный объем приемной емкости (бака), дм3 | 0,5 / 0,3 | 1,7 / 1,1 | 1,8 / 1,2 (12/8) | 1,8 / 1,2 (12/8) | 12/8 |
Габаритные размеры, мм (Длина х Ширина х Высота) | 350х225х300 | 625х375х485 | 630х410х925 | 630х410х925 | 930х410х935 |
Масса/ Масса с ППУ/МПУ, кг | 21/26 | 83 | 135 / 140 | 135 / 140 | 160 / 165 |
Материал диска - карбид кремния / чугун / сталь / комбинированный диск | SiC | ЧХ16М2 / 110Г13Л / Диски со вставками из WC | ЧХ16М2 / 110Г13Л | ||
Модель пульта управления | ППУ ИД 65 | - | МПУ3-04 | МПУ3-04 | МПУ3-06 |
*Зависит от твердости материала и зазора между дисками
**При использовании дисков со вставками из карбида вольфрама
- Эффективное измельчение - использование дисков с рабочими поверхностями двух видов: конусной (для предварительного измельчения) и плоской (для доизмельчения).
- Быстрая очистка - откидная крышка с неподвижным диском обеспечивает быстрый доступ в камеру дробления для сбора пробы, а также - очистки и/или замены дисков.
- Удобство обслуживания - комплектация быстросъемными приемными емкостями, пультами обслуживания и опорными тумбами.
- Точная регулировка - упорная резьба в регулировочном устройстве и контргайка точно и надежно фиксируют выставленный зазор между дисками.
В Дисковом истирателе ИД 65 измельчение происходит за счет истирания – одновременной деформации сжатия и сдвига. Крупность измельченного продукта регулируется величиной зазора между дисками (щели).
В состав истирателя входят: загрузочная воронка, крышка, истирающие диски, корпус, приемная емкость и электродвигатель.
Рабочими органами истирателя являются два диска: подвижный, закрепленный на приводном валу и неподвижный - на крышке истирателя. Крышка закреплена на корпусе, внутри которого расположена приемная емкость. Размер щели задается с помощью шкалы регулировочного устройства. Крутящий момент от электродвигателя на приводной вал передается через ременную передачу.
Принцип работы
Измельчаемый материал подается в загрузочную воронку, откуда через отверстие в центре неподвижного диска поступает в рабочую полость между дисками. В результате действия центробежных сил частицы материала перемещаются от центра к периферии дисков, постепенно измельчаясь.
Предварительное измельчение материала происходит во внутренней конусной зоне, после чего он доизмельчается между плоскими торцевыми участками дисков, образующими калибровочную зону. Крупность частиц измельченного материала определяется расстоянием между дисками (размером щели).
Поток измельченных частиц, исходящий из щели, попадает в приемную емкость.
В процессе работы подвижный и неподвижный диски изнашиваются равномерно. При изменении направления вращения диска эффективность измельчения частиц материала не снижается.
В дисковом истирателе измельчение происходит за счет истирания – одновременной деформации сжатия и сдвига.
В состав истирателя входит: откидная камера с загрузочной и разгрузочной воронками, приемная емкость, стационарная камера, истирающие диски, корпус с приводным валом, рама и электродвигатель.
Крупность частиц конечного продукта определяется зазором между торцевыми поверхностями дисков (щелью). Регулировка расстояния между дисками осуществляется перемещением приводного вала с подвижным диском в осевом направлении.
Рабочая камера истирателя образована внутренней поверхностью откидной камеры и рабочими поверхностями истирающих дисков. Торцевая поверхность дисков на периферии плоская, а вблизи центра имеет сложную клиновидную форму (клиновидная поверхность). Выбранные размеры и углы наклона впадин и зубцов обеспечивают высокую эффективность измельчения и снижают величину нагрузок на детали и узлы в процессе измельчения.
Крутящий момент от электродвигателя передается на приводной вал через ременную передачу.
Принцип работы
Измельчаемый материал подается в загрузочную воронку, откуда через отверстие в откидной камере и в центре неподвижного диска поступает в рабочую полость между дисками. В результате действия центробежных сил, частицы материала движутся от центра к краям дисков, постепенно измельчаясь. Поток измельченных частиц, исходящий из зазора между дисками, попадает в рабочую камеру, где частицы теряют скорость и ссыпаются через разгрузочную воронку в приемную емкость.
Производительность дискового истирателя зависит от физических свойств измельчаемого материала, его размеров на входе и требуемой крупности на выходе (расстояния между дисками).
ВАРИАНТЫ ИСПОЛНЕНИЯ
- Дополнительная комплектация Питателем вибрационным ПГ 1 или ПГ 2;
- Дополнительная комплектация Блоком пылеулавливания БПУ с зонтом.
СПЕЦИСПОЛНЕНИЯ:
- ИД 175 в составе установки (ЩД 10 + ПГ 1 + ИД 175) для измельчения сплавов в среде инертного газа аргона.
В дисковом истирателе измельчение происходит за счет истирания – одновременной деформации сжатия и сдвига.
В состав истирателя входит: откидная камера с загрузочной и разгрузочной воронками, приемная емкость, истирающие диски, корпус с приводным валом, основание и электродвигатель.
Крупность частиц конечного продукта определяется зазором между торцевыми поверхностями дисков (щелью). Регулировка расстояния между дисками осуществляется перемещением вала с подвижным диском в осевом направлении.
Рабочая камера истирателя образована внутренней поверхностью откидной камеры и рабочими поверхностями истирающих дисков. Торцевая поверхность дисков на периферии плоская, а вблизи центра имеет сложную клиновидную форму (клиновидная поверхность). Выбранные размеры и углы наклона впадин и зубцов обеспечивают высокую эффективность измельчения и снижают величину нагрузок на детали и узлы в процессе измельчения.
Принцип работы
Измельчаемый материал подается в загрузочную воронку, откуда через отверстие в откидной камере и центре неподвижного диска поступает в рабочую полость между дисками. В результате действия центробежных сил, частицы материала движутся от центра к краям дисков, постепенно измельчаясь. Поток измельченных частиц, исходящий из зазора между дисками, попадает в рабочую камеру, где частицы теряют скорость и ссыпаются через разгрузочную воронку в приемную емкость.
Производительность дискового истирателя зависит от физических свойств измельчаемого материала, его размеров на входе и требуемой крупности на выходе (расстояния между дисками).
В дисковом истирателе измельчение происходит за счет истирания – одновременной деформации сжатия и сдвига.
В состав истирателя входит: откидная камера с загрузочной и разгрузочной воронками, приемная емкость, стационарная камера, истирающие диски, корпус с приводным валом, рама и электродвигатель.
Крупность частиц конечного продукта определяется зазором между торцевыми поверхностями дисков (щелью). Регулировка расстояния между дисками осуществляется перемещением приводного вала с подвижным диском в осевом направлении.
Рабочая камера истирателя образована внутренней поверхностью откидной камеры и рабочими поверхностями истирающих дисков. Торцевая поверхность дисков на периферии плоская, а вблизи центра имеет сложную клиновидную форму (клиновидная поверхность). Выбранные размеры и углы наклона впадин и зубцов обеспечивают высокую эффективность измельчения и снижают величину нагрузок на детали и узлы в процессе измельчения.
Крутящий момент от электродвигателя передается на приводной вал через ременную передачу.
Принцип работы
Измельчаемый материал подается в загрузочную воронку, откуда через отверстие в откидной камере и центре неподвижного диска поступает в рабочую полость между дисками. В результате действия центробежных сил, частицы материала движутся от центра к краям дисков, постепенно измельчаясь. Поток измельченных частиц, исходящий из зазора между дисками, попадает в рабочую камеру, где частицы теряют скорость и ссыпаются через разгрузочную воронку в приемную емкость.
Производительность дискового истирателя зависит от физических свойств измельчаемого материала, его размеров на входе и требуемой крупности на выходе (расстояния между дисками).
ВАРИАНТЫ ИСПОЛНЕНИЯ
- Дополнительная комплектация Питателем вибрационным ПГ 1 или ПГ 2;
- Дополнительная комплектация Блоком пылеулавливания БПУ с зонтом.
СПЕЦИСПОЛНЕНИЯ:
- ИД 200 в составе установки (ЩД 10 + ПГ 1 + ИД 200) для измельчения сплавов в среде инертного газа аргона.
В дисковом истирателе измельчение происходит за счет истирания – одновременной деформации сжатия и сдвига.
В состав истирателя входит: откидная камера с загрузочной и разгрузочной воронками, приемная емкость, стационарная камера, истирающие диски, корпус с приводным валом, рама и электродвигатель.
Крупность частиц конечного продукта определяется зазором между торцевыми поверхностями дисков (щелью). Регулировка расстояния между дисками осуществляется перемещением приводного вала с подвижным диском в осевом направлении.
Рабочая камера истирателя образована внутренней поверхностью откидной камеры и рабочими поверхностями истирающих дисков. Торцевая поверхность дисков на периферии плоская, а вблизи центра имеет сложную клиновидную форму (клиновидная поверхность). Выбранные размеры и углы наклона впадин и зубцов обеспечивают высокую эффективность измельчения и снижают величину нагрузок на детали и узлы в процессе измельчения.
Крутящий момент от электродвигателя передается на приводной вал через ременную передачу.
Принцип работы
Измельчаемый материал подается в загрузочную воронку, откуда через отверстие в откидной камере и центре неподвижного диска поступает в рабочую полость между дисками. В результате действия центробежных сил, частицы материала движутся от центра к краям дисков, постепенно измельчаясь. Поток измельченных частиц, исходящий из зазора между дисками, попадает в рабочую камеру, где частицы теряют скорость и ссыпаются через разгрузочную воронку в приемную емкость.
Производительность дискового истирателя зависит от физических свойств измельчаемого материала, его размеров на входе и требуемой крупности на выходе (расстояния между дисками).
ВАРИАНТЫ ИСПОЛНЕНИЯ
- Дополнительная комплектация Питателем вибрационным ПГ 1 или ПГ 2;
- Дополнительная комплектация Блоком пылеулавливания БПУ с зонтом.